- Home
- Solutions
- News and Events
- Hilti Blog
- How 'Internet of Things' & cordless tools are driving productivity
How 'Internet of Things' & cordless tools are driving productivity
The importance of big data, not bigger batteries
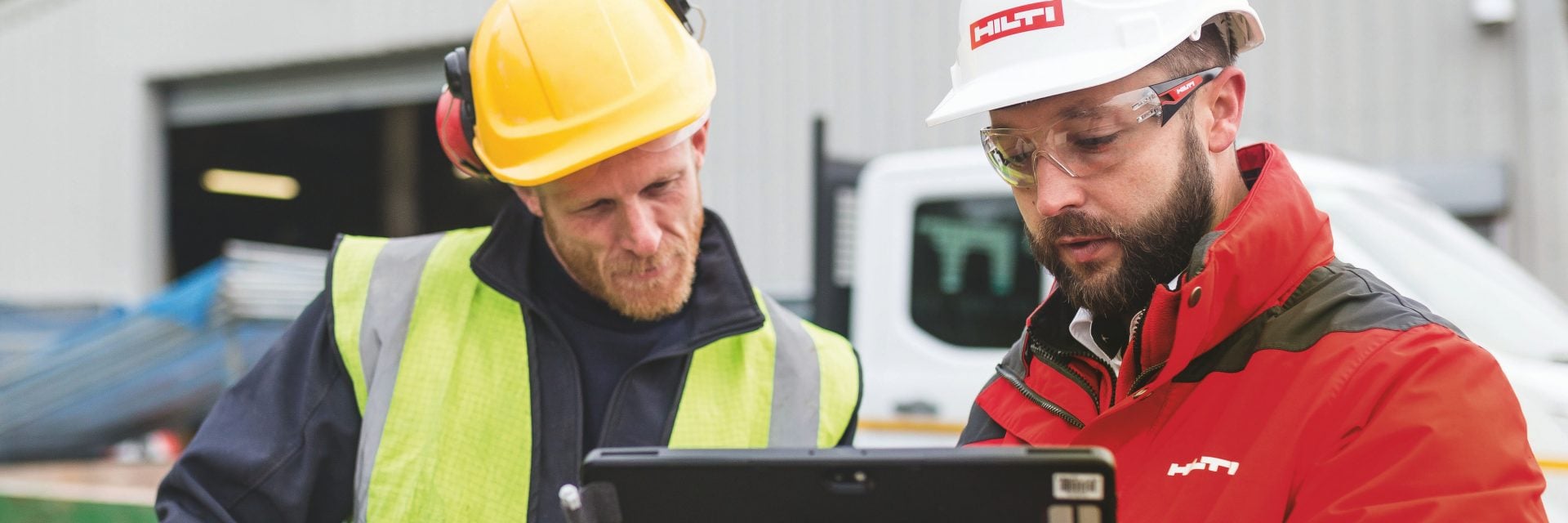
From compact drills to concrete breakers, high-performing cordless tools have become extremely popular on construction sites. In fact, in recent years, cordless tools represented over 50% of the demand for power tools - a figure which will continue to grow every year. [1] This is mostly due to improvements in battery technology that has allowed cordless tools to match the performance and productivity of corded and even gas-powered tools. Workers carrying out medium and heavy-duty work are now benefitting from cordless portability and convenience.
But for managers, cordless equipment can mean more complex tool cribs and compatibility issues. Meanwhile, some manufacturers seem focused on outdoing their competitors with increasingly powerful mega-amp batteries that end up bigger, heavier and more expensive. This neither boosts productivity nor saves money.
So, how should you choose a battery platform? By looking beyond power and performance stats and focusing on its IoT (Internet of Things) and data capabilities. Today’s jobsites generate vast amounts of data waiting to be collected and exploited. Tools and batteries can capture real-time usage data that can be analysed on the back end by software and human experts. This information can help businesses make proactive operational decisions that save money, increase productivity, enhance safety and enable compliance. All it takes is the right kind of battery!
Putting IoT to Work on the Jobsite
IoT has already made inroads on large construction sites, particularly with heavy equipment. Some machines can be controlled remotely with high precision, whilst others use sensors to trigger automated maintenance and usage alerts. Either way, IoT helps companies protect the value of these assets by enabling preventative maintenance while finding ways to increase productivity.
With expensive and heavy equipment, the savings are clear and immediate. But what about power tools? Compared with a loader for example, the outlay of individual tools might seem insignificant. But considering each worker likely has two or more power tools assigned to them (plus shared tools), the aggregate costs - both direct and indirect - can quickly add up. Whether a company has 5 or 5,000 cordless drills, it’s important to know that every single one is providing as much value as possible.
Ask yourself: What’s the real cost of managing your cordless tool crib? After all, there are direct costs from purchasing, repairs, maintenance and calibration, and indirect costs from time spent procuring tools, managing failures and tracking down lost equipment. And when a battery or tool starts underperforming over time, incremental productivity decreases can go painfully undetected.
So, while construction booms, demand increases and timelines shrink, management becomes more complex. Suddenly traditional processes – like paper trails, incompatible technology and siloed platforms – are woefully insufficient. All this hurts the bottom line.
This is where IoT can help. Smart batteries and tools that capture jobsite data can digitise processes in the back end, enabling you to manage costs better while keeping your teams working productively.
IoT & Power Tools: Innovation or Gimmick?
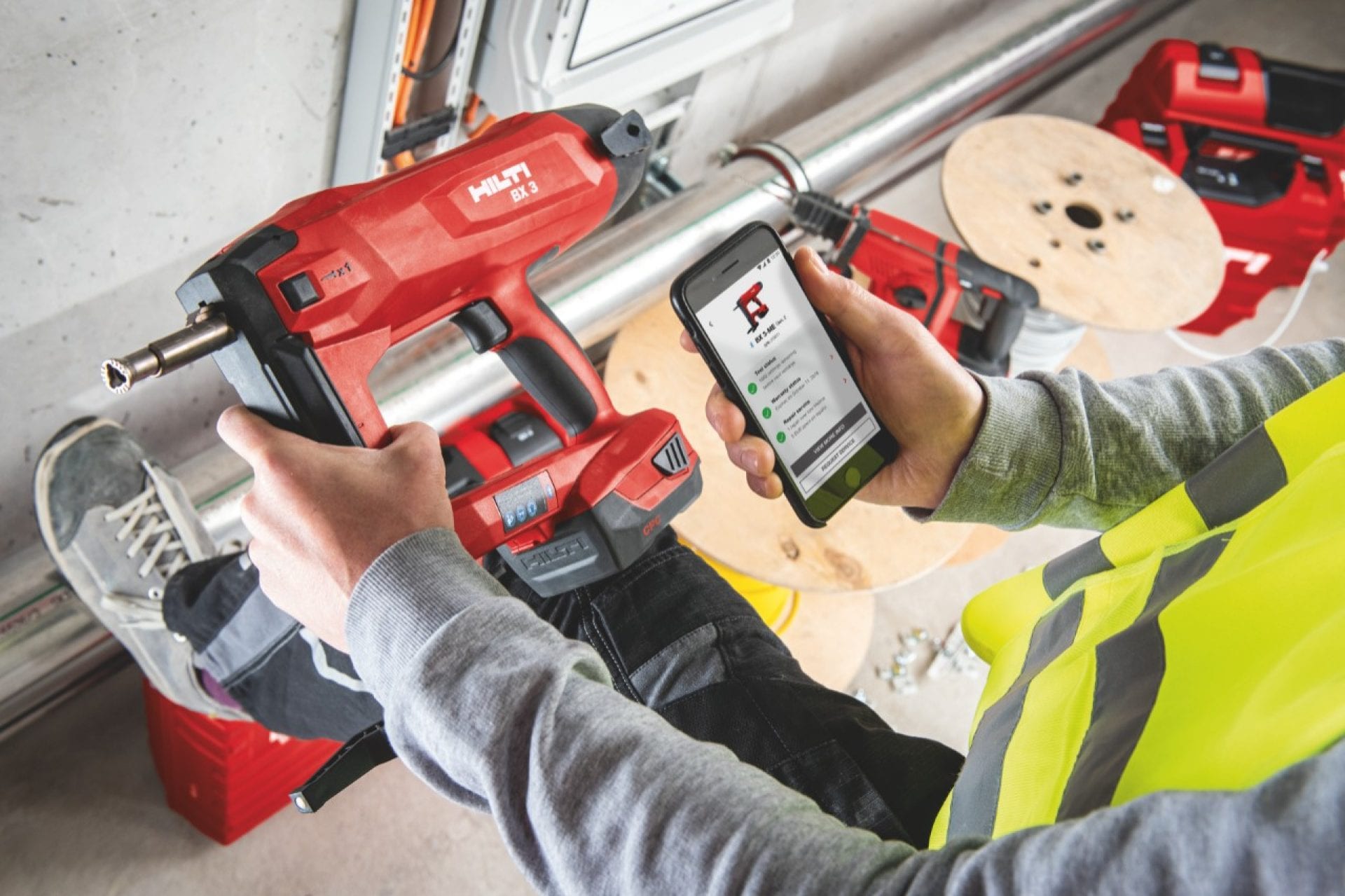
Today, everything is “smart” and “connected” - from cars and TVs, to light bulbs and toasters. It seems some manufacturers have pushed the “things” part of IoT as far as it can go, often into places that provide no value. Likewise, most major power tool brands have incorporated some form of IoT into their cordless platforms. But just because a tool can be connected doesn’t mean it should be.
IoT on power tools can sometimes be gadgetry. Instead of increasing productivity (which is the point), it can slow teams down. For example, workers might have to juggle multiple platforms, each with its own smartphone app. Instead of a more productive jobsite, you’ve got workers standing around looking at their phones. Connected solutions shouldn’t just exist for the sake of it, but rather to make power tools more productive.
of technical staff in Ireland
have a doctorate degree in computer science, electrical engineering, maths or a related field [1]
fastest broadband speeds in the world
Ireland is now one of the world’s premier locations for data centres thanks to its ideal air-cooling climate [2]
year on year increase by users in Ireland
Adoption of IoT technologies by businesses continues to rise in the Republic [3]
longer for large jobs to be finished
Large projects are taking up to 20% longer to finish than scheduled and are up to 80% over budget [4]
Capturing Data in Real Time
Some manufacturers build IoT directly into the tool. Others put it in the battery, creating a fully connected ecosystem comprising any tool on the platform. IoT-connected smart tools can capture real-time jobsite data such as:
- Where the tool is
- Who it’s assigned to
- How it’s being used
- Whether it’s being used properly and safely
- How often it’s being used
- Whether it’s idle
- Battery health and tool performance
- Any conditions detrimental to productivity, such as overloading
This data can be delivered directly to the user as an update (such as tool or battery state of health) or to provide personalised recommendations - such as torque and speed settings for specific fasteners and base materials.
But the real power comes when jobsite data uploads to the cloud for back end analysis. This could happen when the battery is plugged into the charger, which allows for an uninterrupted transfer that requires no additional intervention from the worker. But whatever platform a contractor chooses, it should be a single ecosystem with seamless connectivity between the tools and the cloud.
Turning Data Into Business Value
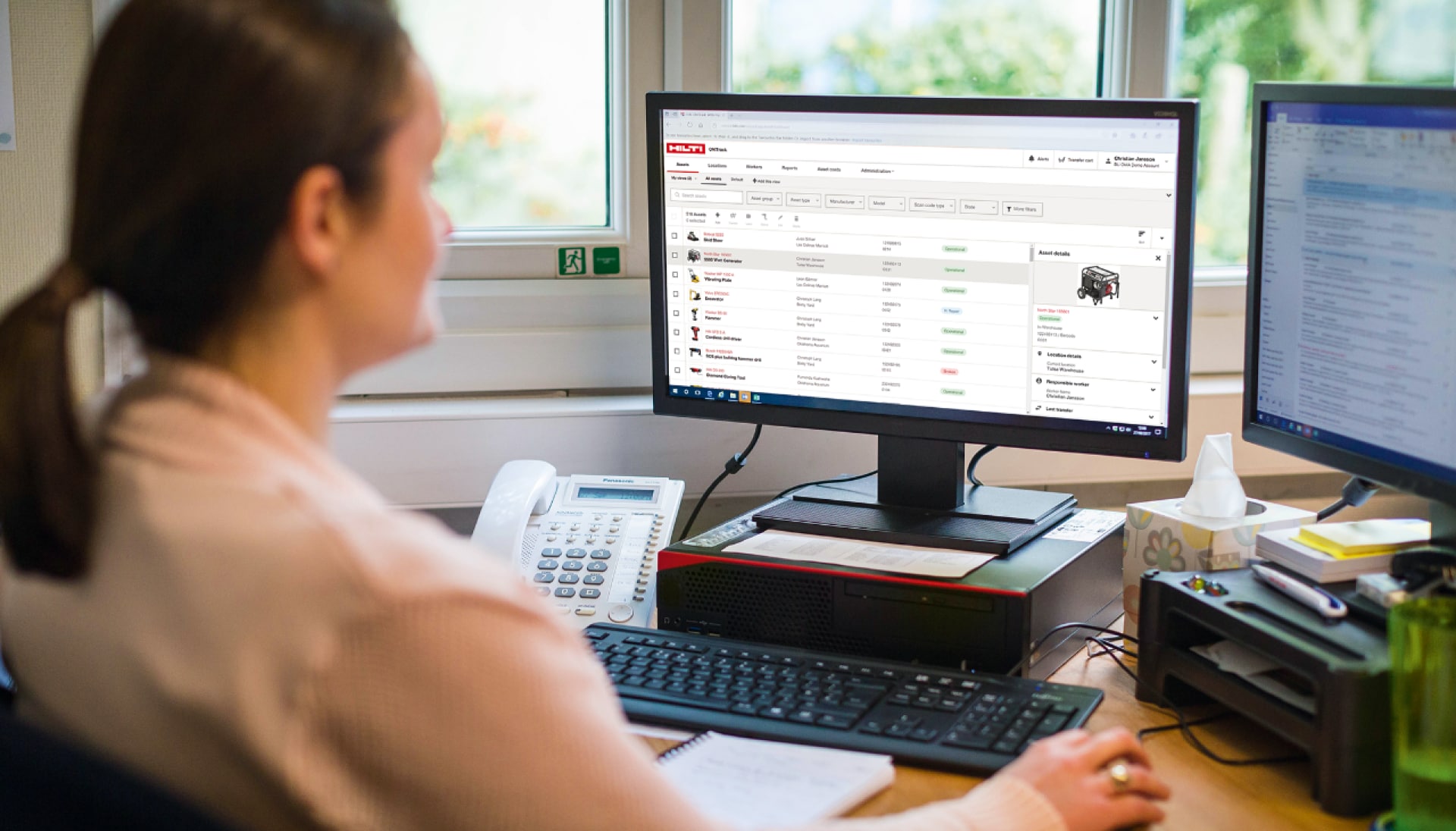
Once uploaded to the cloud, stakeholders onsite, in the office or at home can use this captured data to measure project success, uncover hidden costs or make business decisions that improve productivity, enhance safety and make tool management more efficient.
Some construction management apps use equipment data to steer jobsite quality, compliance and safety by documenting tool usage. Project managers can generate reports that demonstrate the accuracy and progress of their team’s work to inspectors or superiors. They can proactively keep on top of certification paperwork by receiving alerts when workers need to renew tool qualifications or attend training. And they might get notified when a worker is approaching the maximum allowable trigger time on a tool.
Asset management software uses jobsite data to enhance control over inventory and costs by providing real-time transparency of equipment. For example, the software can proactively alert stakeholders when an underperforming tool needs repairing or replacing, or when equipment needs testing, maintenance or calibration. Combine these notifications with a tool management programme, and otherwise time-consuming processes become seamless or automated.
Operations managers can also do live inventory checks at storage locations and gather last-known location information. When a worker requests a tool, the manager can quickly identify idle equipment and get it onto the jobsite straight away. And if a tool goes missing, the manager can locate it and remotely lock its functionality if necessary.
Big Data’s Role in the Future of Construction
Merely adopting a cloud-based platform that can process information in real time can increase productivity substantially. For many, collecting jobsite data and analysing it in a meaningful, actionable way is the first step towards achieving growth in this area.
Of course, all that data is useless – or worse, misleading – if it isn't appropriately analysed and presented. That’s why the best data-driven services have flexible cloud-based dashboards that are easy to use and understand. They also offer more reliable customer support teams to address any complex questions that could arise.
Some service providers can arrange consultations to assess raw data and provide insights into whether businesses have the best-equipped, most productive tools for their projects. They can help calculate the real cost of the equipment and identify wasteful spending on duplicate or unnecessary tools. Armed with industry knowledge, they can help establish meaningful benchmarks by comparing a company’s tool usage data with that of its competitors.
Investments in future-proofing a business with IoT-equipped cordless tools and data-driven services can return huge dividends in the near and long term. Some providers even offer implementation services. Contractors already using cordless tools are likely an upgrade away from unlocking major productivity gains with IoT.
To learn more about how Hilti’s data-driven services can help your business please fill out the form below and a member of our team will call you to discuss next steps!
Alternatively, you can register with us online and sign up to receive our newsletter - which contains exclusive updates on our latest technology and innovations.
(Already have an online account with us? You can manage your newsletter preferences here)