5 ways to reduce jobsite accidents
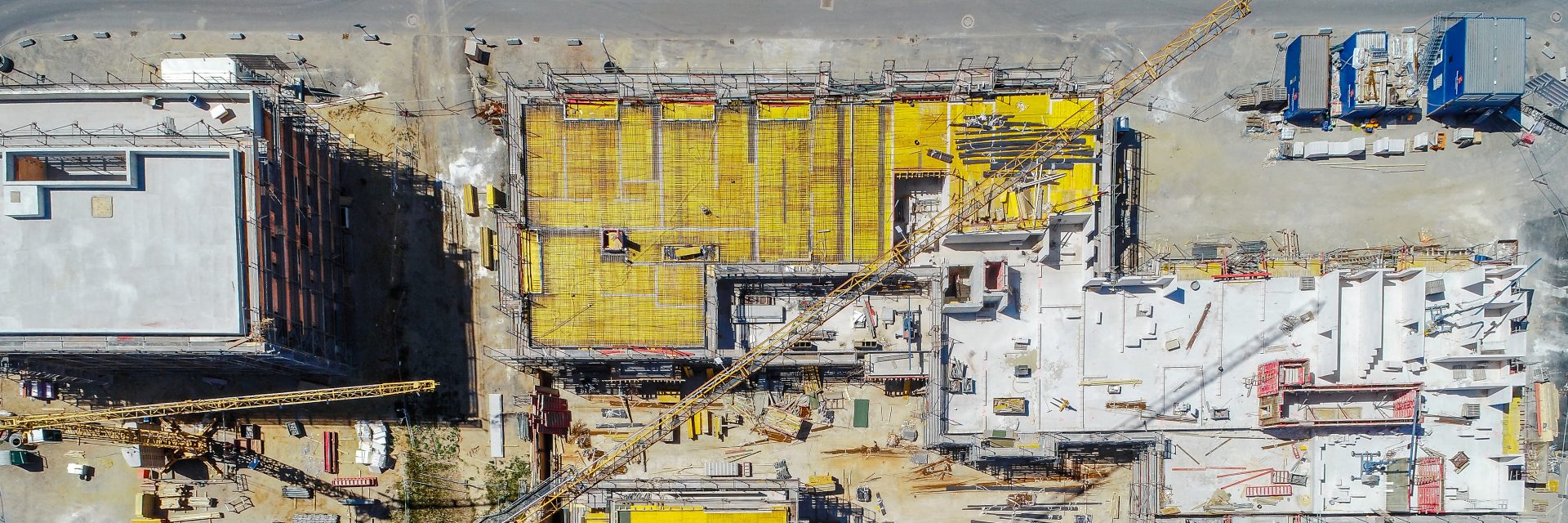
3. Provide health & safety training
Preventing injuries on-site requires more than just good housekeeping - it requires employees to be constantly aware of the dangers around them. As an employer, you must go above and beyond obligation (basic regulations and requirements) to provide workers with the health and safety knowledge they need to feel comfortable and valued on-site.
It's important for workers to be expertly trained on planned emergency procedures, as well as general on-site precautions. A good way to do this is with the STOP! Principle, which provides practical strategies to reduce the impact of things like dust, vibration and kickback. This is a simple and effective way to implement proper health and safety training, that employees will be able to remember and use if a situation arises.
Problems arise when safety isn’t regularly communicated to workers, so make sure you're always keeping them in the loop.
Other Blogs You May Be Interested In
Share